Szabadalmi oltalmaik lejárta után a különféle additív technológiák hamarosan a katonai életben is megjelentek. Összegyűjtöttük, hogy a külföldi haderők – az alkatrészgyártástól a tankon és a golyóálló mellényen át a gránátvetőig, valamint a tengeralattjáróig – mi mindenhez használták már a 3D nyomtatást.
A Nemzeti Közszolgálati Egyetem (NKE) a katonai, valamint a biztonság- és védelempolitikai felsőoktatás tudáscentruma Magyarországon. Az NKE Hadtudományi és Honvédtisztképző Kara idehaza az egyetlen katonai felsőoktatást folytató intézmény, amely a Magyar Honvédség haderőnemei számára képez vezetői utánpótlást. Az egyetemen és a honvédségben is egyre nagyobb hangsúlyt kapnak a katonai célú kutatások, továbbá a védelmi innovációk, ezeken belül pedig az additív gyártási eljárások. (A technológia történetét ötrészes sorozatban mutattuk be.)
Az alábbiakban összegyűjtöttük, a külföldi haderők az elmúlt tíz évben mire használták a 3D nyomtatást. A hadászati alkalmazások kronológiai sorrendje bemutatja az egyre szélesedő felhasználási területeket, egyúttal jellemzi a hadiipar térbeli nyomtatási (3DP-s) technológiájának fejlődését. A megoldások közül némelyik a civil szféra különböző területein is kitűnően alkalmazható.
2013 – Alkatrészgyártás a harctéren
Az amerikai hadsereg mobil fablab-okat (fabrication laboratory-kat, azaz mozgó műhelyeket) készített és alkalmazott Afganisztánban. A hatméteres konténerek, vagyis az ELM-ek (Expeditionary Lab Mobile, expedíciós mobil műhelyek) műholdas kapcsolattal, generátorral, fűtő- és hűtőrendszerrel, CNC maróval, lézer- és plazmatechnológiával, valamint 3D nyomtatókkal rendelkeztek. A műhelyekben két speciális képzettségű mérnök vezetésével műanyag, alumínium és acél alkatrészeket gyártottak a harctéren.
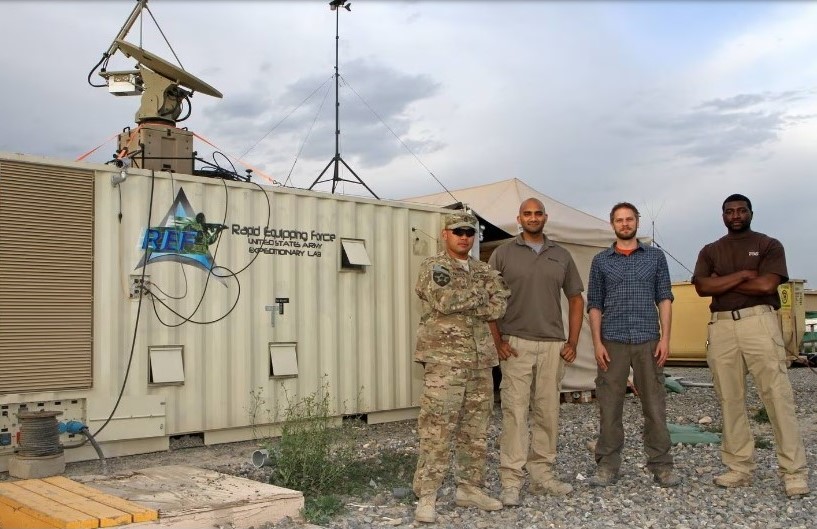
2014 – Terepszemle
A kínai katonaság 3D nyomtatással készítette el Lanzhou város részletes taktikai tereptérképét. A katonai szakértők szerint az ilyen domborzati térképek nagy segítséget adtak a földrajzi viszonyok megértéséhez. A városról gyorsan és olcsón előállított 3D-s modellek pontosabbak elődeiknél, a topográfiai jegyeket pedig változatos színekben (full colorban) jelenítették meg. A máskor hetekig tartó munkát mindössze nyolc óra alatt befejezték. Ráadásul az A4-es méretű nyomtatott térképek könnyűek, így a szállításuk is egyszerű.
2014 – Bionyomtatás a gyógyulásért
Az amerikai védelmi minisztérium által alapított intézet, az AFIRM (Armed Forces Institute of Regenerative Medicine) klinikai terápiák fejlesztésével, bőrgyógyászattal, emberi sejtek, szövetek és szervek regenerálásával foglalkozik. A kidolgozott gyógyítási folyamat a következő: a kutatók a sebet vagy az égési sérülést beszkennelték, majd 3D-s képet készítettek róla. Ezt követően a bionyomtatót feltöltötték kétféle bőrsejttöltettel, egy számítógépes szoftver pedig meghatározta, hol kezdjék a nyomtatást és melyik sejttípust alkalmazzák. A nyomtató mindegyik sejtet hajszálpontosan oda printelte, ahova kellett. A sejtek aztán növekedésnek indultak, idővel pedig új bőr képződött a sérült helyeken.
2015 – Tank és alkatrészei
Az orosz hadsereg egyik gyártó cége, az Electromashina JSC nyilvánosságra hozta, hogy ipari 3D nyomtatót használt a T-14 Armata tankhoz. A vállalat mestermodelleket készített térbeli nyomtatással, továbbá a harckocsihoz fém- és műanyagrészeket is printeltek.
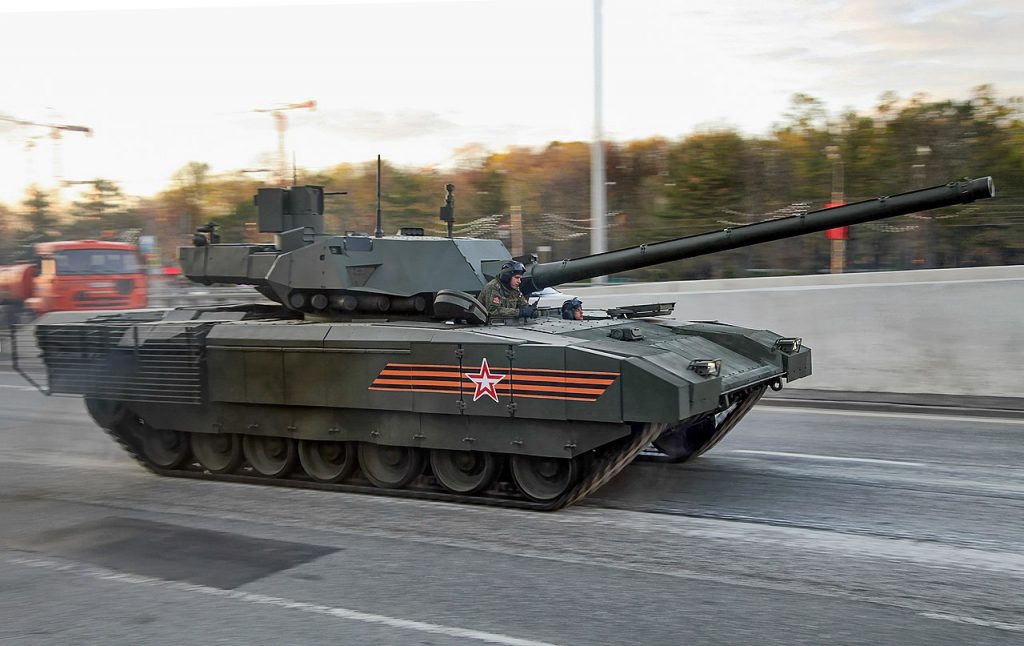
2015 – Harci repülők javítása
Az amerikai légierő a pilóta nélküli X-47B harci repülőgép landolását tesztelte, mert súlyos problémák adódtak a farok elfogóhorgával, amely állandóan leszakadt. A helyszínen lévő műszaki szakemberek véleménye szerint a javítás egymillió dollárba került volna, a szükséges munka időtartamát pedig legalább 8 hónapra becsülték. Emiatt segítséget kértek a légierő egyik speciális javítóműhelyétől, ahol már akkor is naprakész csúcstechnológiákkal, köztük három 3D nyomtatóval dolgoztak. Végül a problémás elfogóhorgot teljesen egyedi darabbá alakították át. A munkát egy nap alatt elvégezték, az alkatrész pedig mindössze 240 dollárba került.
2015 – Golyóálló mellény
A következő kiemelést érdemlő fejlesztés amerikai és izraeli kutatók nevéhez fűződik, akik újfajta, halpikkelyes golyóálló mellényt készítettek. A printelt védőfelszerelés egyszerre merev és rugalmas, akárcsak a természetből vett minta, ugyanis a merev lemezekből készült külső rétegek alá további rugalmas rétegeket terveztek. A mellényt szimultán többanyag-nyomtatásra alkalmas Stratasys Objet500 Connex géppel készítették. A felszerelés előnye, hogy személyre szabható, a küldetéstől függően specifikusan alakítható. A mellény viselője nagyobb biztonságban van, mint az eddigi szabvány szerint, kevlárból készült darabokban.
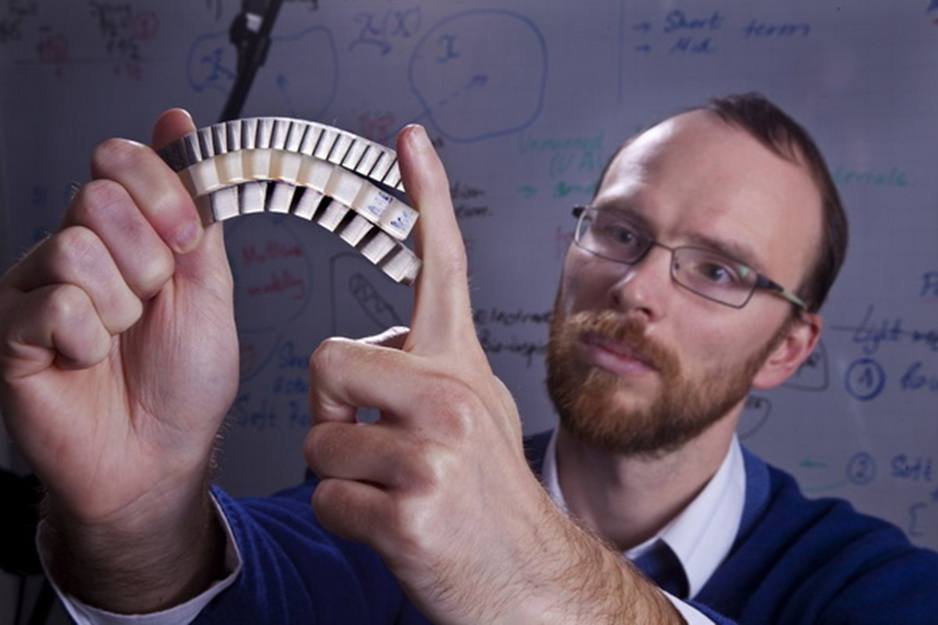
2016 – Fegyverek, lövedékek
A legendás Kalasnyikov hadiipari cég 2016 februárjában jelentette be, hogy új gépkarabélyának egyes részeit 3D fémnyomtatással gyártja. A Távlati Kutatások Orosz Alapítványa később arról számolt be, hogy sikeresen tesztelték a printelt lőszereket, amelyek több szempontból is ugyanolyan eredményt értek el, mint a hagyományos módszerrel előállítottak.
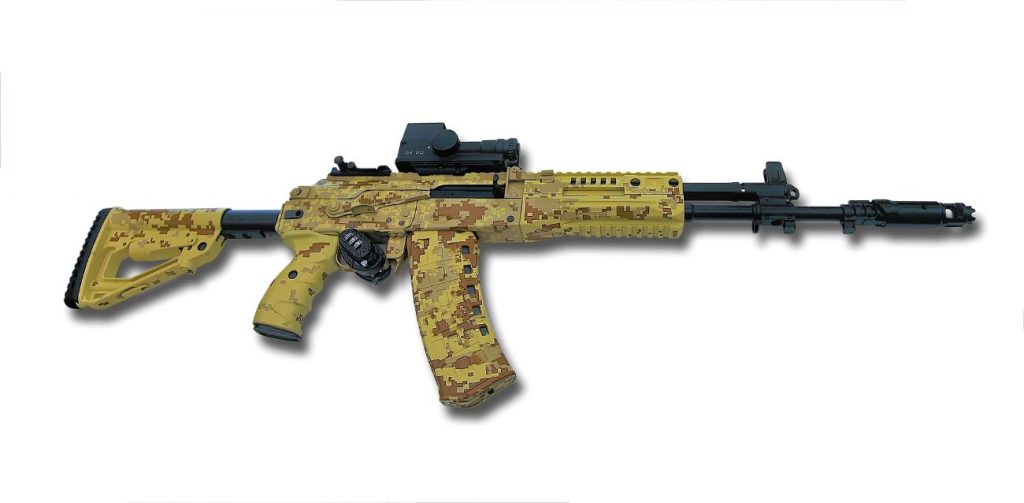
2017 – Drónok egy nap alatt
Az amerikai hadsereg kutatólaborja (ARL) a 3DP és a pilóta nélküli járműtechnológia (UAV) összekapcsolásával akár 24 óra alatt bármilyen feladatra automatikusan konfigurálható és optimalizálható drónokat nyomtatott. Az így készített drónok alkalmasak légi megfigyelésre, kommunikációra és szállításra is.
2017 – Repülőmotor
A General Electric (GE) Aviation a nikkelalapú ötvözeteknél 50 százalékkal könnyebb titán-alumínium (TiAl) ötvözetből lapátokat nyomtatott az eddigi legnagyobb sugárhajtóművéhez. A GE9X alacsony nyomású turbina, több mint 2 méter átmérőjű. A lapátok négyszer vékonyabbak, mint ha lézeres 3D printeren készültek volna. Az elektronsugaras technika gyorsaságban vetekszik a TiAl részek gyártási szabványának számító öntéssel. Ráadásul ugyanazon a gépen megváltoztatható az alkatrész formája, így egyszerre készíthetők különféle lapátok. A cég számára a 3DP azért is bizonyult tökéletes megoldásnak, mert 800 alkatrészt 12 egységbe tudtak összerakni. Emellett a technológia és a termék sokkal inkább környezetbarát, mint a hagyományos gyártási eljárások.
2017 – Gránátvető
Az amerikai hadsereg RAMBO (Rapid Additively Manufactured Ballistics Ordnance) nevű, saját fejlesztésű nyomtatott gránátvetőt tesztelt. A RAMBO-t teljes egészében fémporból készítették. Beszámolók alapján a fegyver esetében előírt 15 tesztet kivétel nélkül sikerrel hajtották végre.
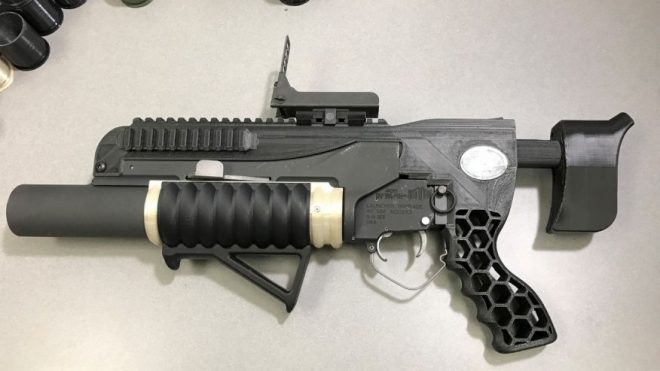
2017 – Tengeralattjáró
Az Oak Ridge Nemzeti Laboratórium (ORNL) és partnere, a Haditengerészet Diszruptív Technológiai Laboratórium 10 méter hosszú tengeralattjárót nyomtatott. A hajótest az ORNL Big Area Additive Manufacturing és a Cincinnati Inc. közösen fejlesztett 3D printerén, szénszálból készült. A gyártás hónapok helyett mindössze napokig tartott. Emellett fontos hangsúlyozni, hogy alapesetben a tengeralattjárók építése nagyon költséges: csak maga a hajótest 600–800 ezer dollárba kerül. Ehhez képest a haditengerészet és az ORNL szakemberei szerint térbeli nyomtatással az előállítási költségek akár 90 százalékkal csökkenthetők.
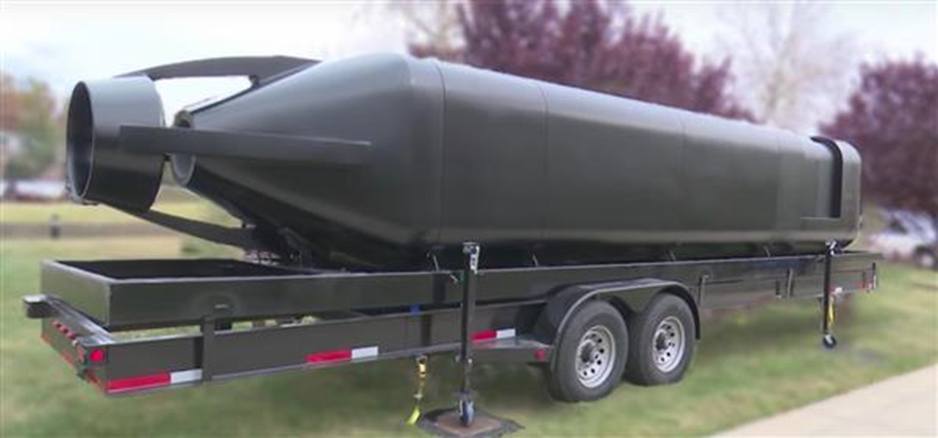
2018 – Légcsavarszárny
A francia haditengerészet, a Védelmi Tengerészeti Csoport és a Nantes-i Egyetem mérnökei bonyolult geometriájú, 300 kilogrammos légcsavarszárnyat készítettek, méghozzá úgynevezett drótíves additív gyártással (Wire Arc Additive Manufacturing, WAAM). A huzalívadalékos technológiával gyorsan, igencsak nagyméretű és tömegű alkatrészek gyárthatók titánból, acélból, bronzból, nikkelből vagy alumíniumból.
A következő részben a 2018-tól napjainkig tartó időszak különleges katonai 3DP-s megoldásait, alkalmazásait mutatjuk be.