Az additív technológiák néhány éve valósággal új kaput nyitottak az űrben történő gyártáshoz. A 3D nyomtatás segítségével pedig egyre közelebb kerülünk az emberiség egyik nagy álmához, a Földön kívüli környezetben fenntartható lét megvalósításához. A közelmúlt legjelentősebb eredményeit foglaljuk össze.
Sorozatunk előző részében többek között az első űrben nyomtatott szerszámról, valamint arról is olvashattak, milyen műanyagokból lehet tárgyakat készíteni a Nemzetközi Űrállomáson (az ISS-en). Ezúttal az űreszközök ugrásszerű fejlődését mutatjuk be az elmúlt 6 év távlatában.
Mélyűri szonda (2018)
A NASA Orion mélyűri (bolygóközi) szondája a Stratasys, a Phoenix Analysis & Design Technologies és a Lockheed Martin Space közös erőfeszítésének köszönhetően 100 nyomtatott alkatrészből készült. A dokkolónyílás ajtaját szintén 3D-ben printelték, méghozzá az amerikai Stratasys Antero 800NA alapanyagából. A szonda feladata a személyzet nélküli, Holdon túli küldetés végrehajtása volt.
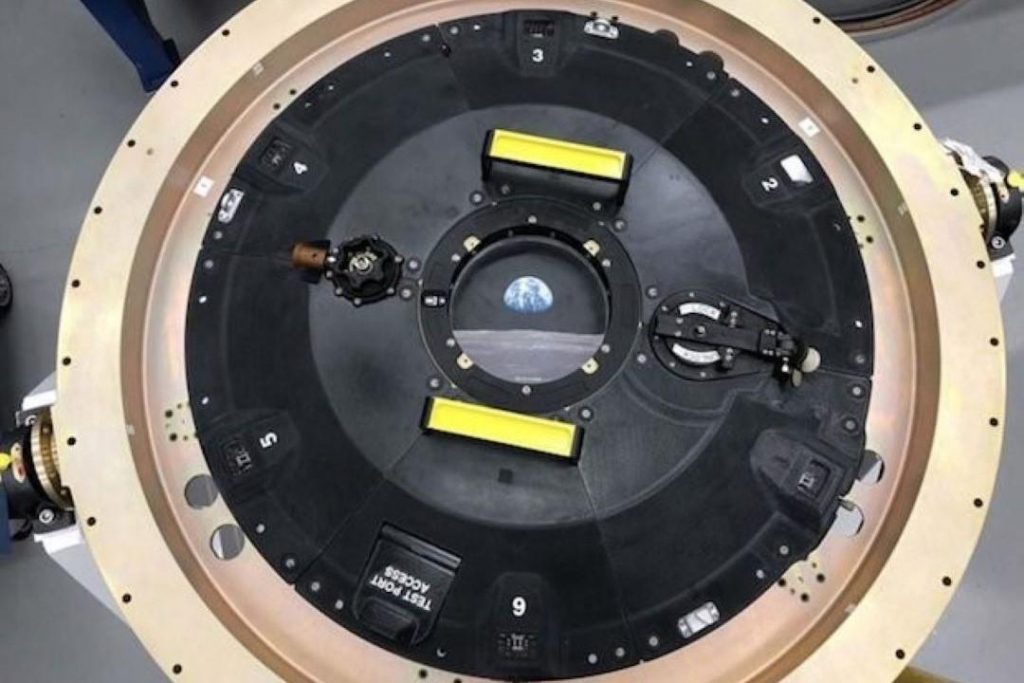
Újrahasznosító berendezés (2019)
A NASA Marshall Űrrepülési Központja, az In-Space Manufacturing és a Tethers Unlimited Firmamentum részleg elkészítette a Refabricator nevű berendezést, amely egy műanyag újrahasznosító és egy 3D printer kombinációja. A gép segítségével az űrhajósok az ISS műanyaghulladékát nyomtatószállá alakították át, ebből pedig egyebek mellett új alkatrészeket, orvosi eszközöket, valamint edényeket készítettek.
Oxigén-előállítás a Marson (2021)
A Mars légkörének 96 százaléka szén-dioxid. Az Egyesült Államokban kifejlesztettek egy berendezést, a MOXIE-t (angolul: Mars Oxygen In-Situ Resource Utilization Experiment-et), amely a Mars légkörében lévő szén-dioxidból oxigént állított elő. A Perseverance nevű rover (marsautó) 2021-ben landolt a MOXIE-val a vörös bolygón. Az eszköz a térbeli nyomtatás nélkül nem is működhetne. A speciális nikkelötvözetű alapanyagból csak 3D nyomtatással lehet előállítani a hőcserélőt, amely felmelegíti és lehűti a rajta átáramló gázokat. Így a printelt alkatrészek kibírják a nagy nyomást és a rendkívüli hőterhelést.
A berendezés – hasonlóan egy kisebb méretű fához – óránként 6–10 gramm, 98 százalékos tisztaságú oxigént termelt. Ez a mennyiség egy űrhajós számára 10 percig elegendő. Az előállított oxigént egyébként az üzemanyagellátáshoz használták. A MOXIE működése során összesen 122 gramm oxigént termelt. Csak összehasonlításképpen: ez körülbelül akkora mennyiség, amennyit egy kiskutya 10 óra alatt lélegez be.
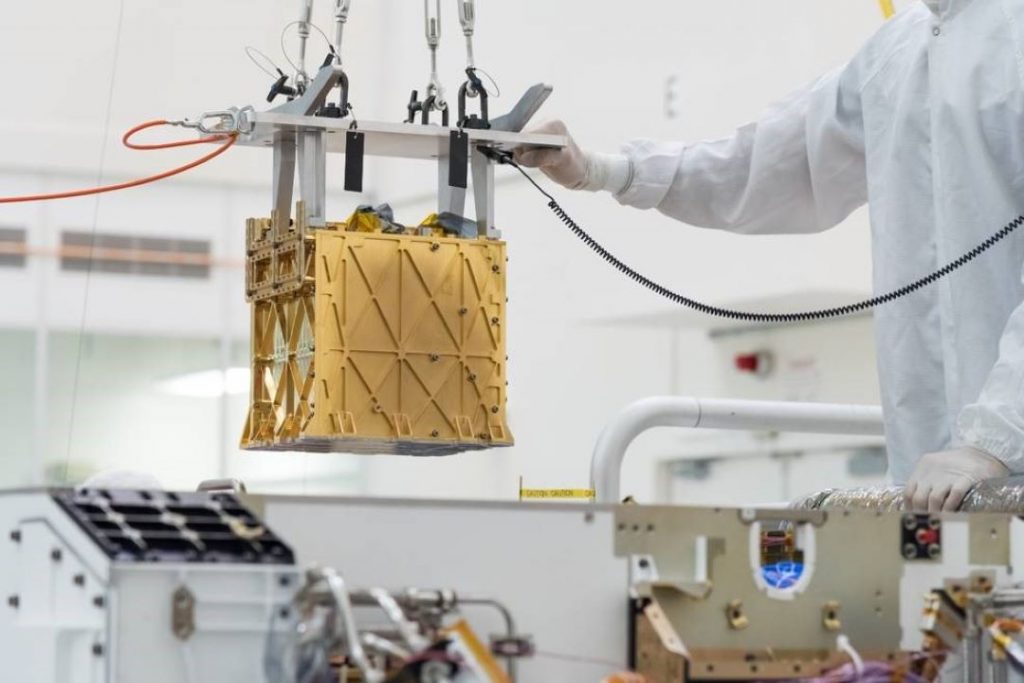
A floridai Cape Canaveral űrközpontból 2023. március 23-án fellőtték a világ első olyan rakétáját, amely össztömegének 85 százaléka 3D nyomtatással készült alkatrészekből állt. A Relativity Space startup cég Terran–1-es, kétfokozatú, újrafelhasználható rakétája a „jövő üzemanyagával” (folyékony oxigénnel és folyékony földgázzal) működő Aeon nyomtatott hajtóművel emelkedett a magasba. A rakéta 33,5 méter hosszú és 2,28 méter átmérőjű volt. A Terran–1-et, a Stargate mesterséges intelligencia segítségével, hatalmas méretű speciális fémötvözetekkel dolgozó 3D nyomtatókkal állították elő. A startup jövőbeli célja, hogy a rakéta 95 százaléka ezzel az eljárással épüljön meg.
Mars-szimulátor (2023)
Ugyanebben az évben a NASA – világelsőként – 3D-ben nyomtatott, 1700 négyzetméteres szimulációs marsi környezetet hozott létre a texasi Houston Johnson Űrközpontban. A terveket a Bjarke Ingels Group készítette, a kivitelező az Icon cég volt. 2023. június 25-én négy fő kezdte meg a 378 napig tartó projektet, amelyben a marsi űrmissziók lehetőségeit tesztelték. A személyzet a 158 négyzetméteres, 3D-ben printelt „Mars Dune Alpha” lakóhelyen élt. A négy kiválasztott ember zöldségeket termesztett és takarított be, karbantartási feladatokat végzett, sétált a szimulált vörös bolygón, továbbá kipróbálta a Földdel való kommunikációs zavarok esetén megvalósítandó teendőket. A külvilágtól elzárt résztvevők ízelítőt kaptak a fenntartható földi létből is.
Bionyomtatás a Nemzetközi Űrállomáson (2023)
A Redwire, a bionyomtatás úttörő vállalata által kifejlesztett 3D BioFabrication Facility (BFF) technológiát tesztelték az ISS-en 2023 szeptemberében. Végül sikeresen kinyomtatták az első emberi térdgyűrűporcot (meniszkuszt). A szövetmintát elemzés céljából később visszahozták a Földre. A Redwire ezzel a projekttel tavaly egészség kategóriában rangos díjat nyert.
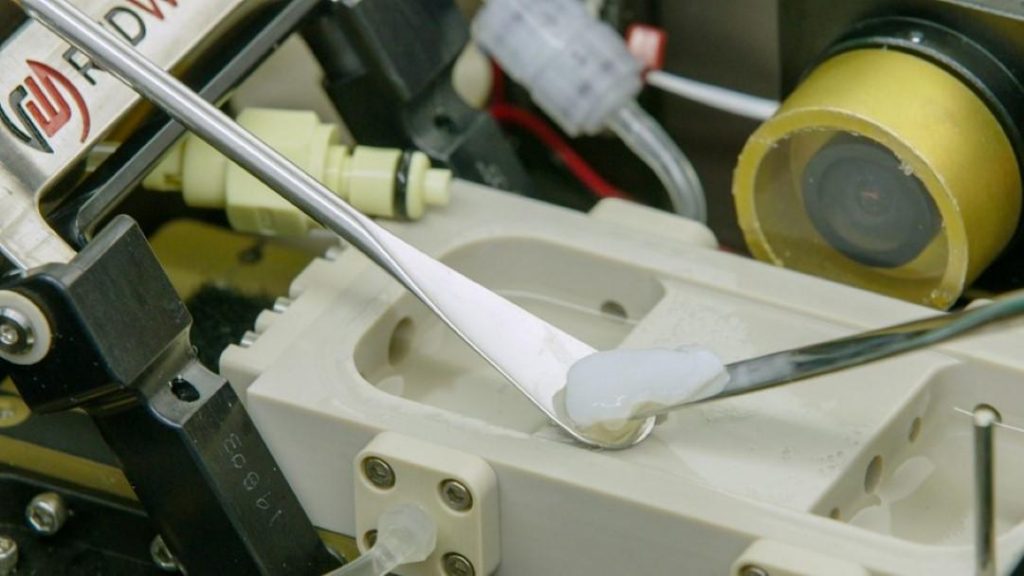
Fémnyomtatás (2024)
A francia multinacionális vállalat, az AddUp, valamint az Airbus Védelem és Világűr részlege elkészítette az Európai Űrügynökség (ESA) első fémprinterét. Mivel a fémalkatrészeknek a Földről az ISS-re történő elszállítása akár 12 hónapig is tarthat, az ESA kérte a fémnyomtató elkészítését. A berendezést végül az ISS Kolumbusz Európai Tudományos Modulján installálták. Idén május utolsó hetében pedig, az emberiség történetében először, az ESA fémet nyomtatott a világűrben. A printerrel a nagyteljesítményű lézertechnológiát rozsdamentes acélhuzallal kombinálva készítették el az első fémnyomatot.
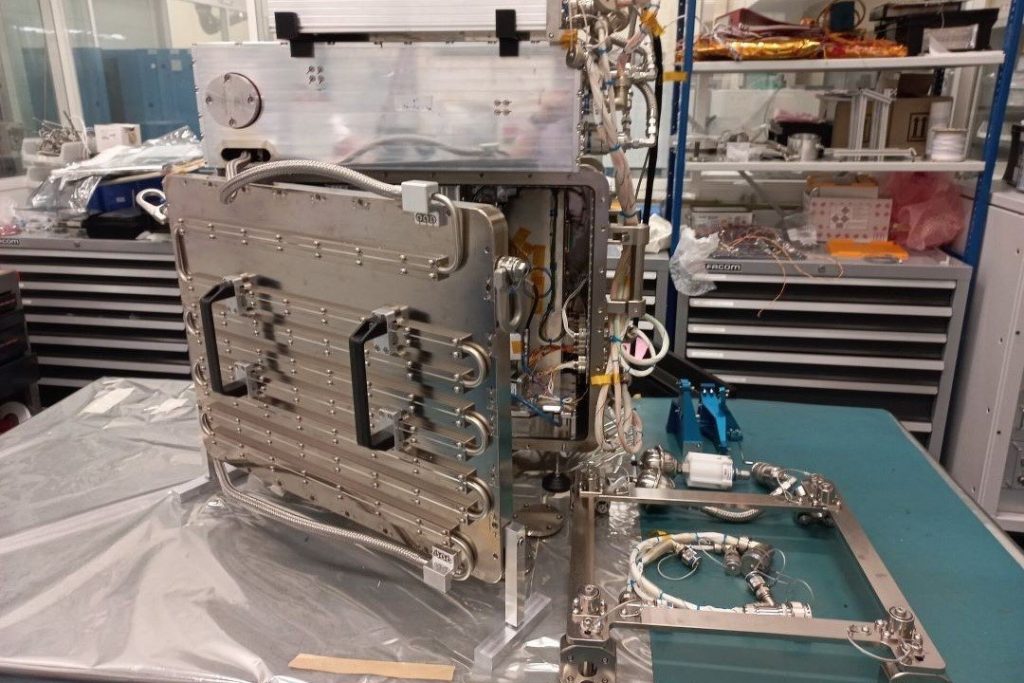
A munkát az ESA, az Airbus és a CNES (a francia űrügynökség) kutatói a Földről felügyelték. A kísérlet igazolta, hogy mikrogravitációs környezetben is elő lehet állítani összetett fémszerkezeteket. Sébastien Girault, a projekt rendszermérnöke szerint a nyomtatás minősége messze felülmúlta várakozásaikat. Az űrben printelt próbatesteket és a Földön készítetteket egyaránt tesztelik, mert szeretnék megtudni, melyikek rendelkeznek jobb mechanikai tulajdonságokkal.
Szoftverek az űrkutatás szolgálatában (2024)
Eddig kevés szó esett a 3D technológia szellemi hátteréről, pedig e nélkül használhatatlan lenne ez a modern gyártási eljárás. Az űriparban a 3D nyomtatási technológiát alkalmazó vállalatok, mint az egyesült államokbeli, az űrmeghajtáshoz toló- és rakétahajtóműveket gyártó Agile Space Industries, valamint az űrkutató cégek, mint az Astrobotic vagy az ispace, egyaránt használják a legfejlettebb szoftvert, az Oqton 3DXpert-et. Ezzel a szoftverrel rekordidő alatt képesek küldetéskritikus alkatrészeket fejleszteni.
A szoftver a gyártás elején teljes körű folyamatvezérlést biztosít, de később a mérnökök, ha szükséges, változtatásokat végezhetnek. Az Oqton 3DXpert-tel a 3D-s modellek STL fájllá (nyomtatható modellfájllá) alakítás nélkül szeletelhetők. Így nem áll fenn az a veszély, hogy eltérések történnek az eredeti geometriától. További hatalmas előny, hogy amíg korábban a gyártás, az összeszerelés és a tesztelés évekig tartott, addig a program révén ezek a folyamatok már hetek alatt elvégezhetők. Ráadásul a szoftver kevesebb RAM-ot (operatív memóriát) igényel.
Mint az a fentiekből kiderül, az űrkutatással foglalkozó szakemberek az elmúlt években nemcsak felfedezték maguknak a 3D nyomtatást, hanem egyre több területen bátran alkalmazzák is. A technológia gyors fejlődését látva a határ pedig tényleg a csillagos ég.
A nyitókép forrása: depositphotos.com