Mi volt az első űrben nyomtatott szerszám? Milyen műanyagokból lehet tárgyakat készíteni a Nemzetközi Űrállomáson? És valóban legyártható egy teherhordó rakéta akár három nap alatt? Egyebek mellett ezekre a kérdésekre is megadjuk a választ legújabb írásunkban.
Korábbi cikkünkben az űrkutatás kiemelkedő magyar tervezőmérnökeinek munkásságát elevenítettük fel, ezúttal pedig bemutatjuk, a térbeli nyomtatás hogyan tudta meghódítani a világűrt. Ez az additív technológia ugyanis néhány éve valósággal új kaput nyitott az űrben történő gyártáshoz. Így aztán egyre közelebb kerülünk az emberiség egyik nagy álmához, a Földön kívüli környezetben fenntartható lét megvalósításához. Nézzük, hol tartunk ezen a felfedezőúton!
Nyomtatás mikrogravitációs környezetben
A 3D nyomtatás szabadalmi védettségeinek lejárta után a technológia az űrkutatásban is dinamikusan fejlődött. A floridai székhelyű Made in Space Incorporation a NASA (National Aeronautics and Space Administration, az Egyesült Államok Nemzeti Repülési és Űrhajózási Hivatala) megbízásából 2010-ben kezdte meg az első, mikrogravitációs használatra alkalmas 3D printer kifejlesztését. A vállalkozás a Fused Filament Fabrication (FFF) technológiát, azaz a műanyagszál-olvasztásos eljárást választotta a megvalósításhoz.
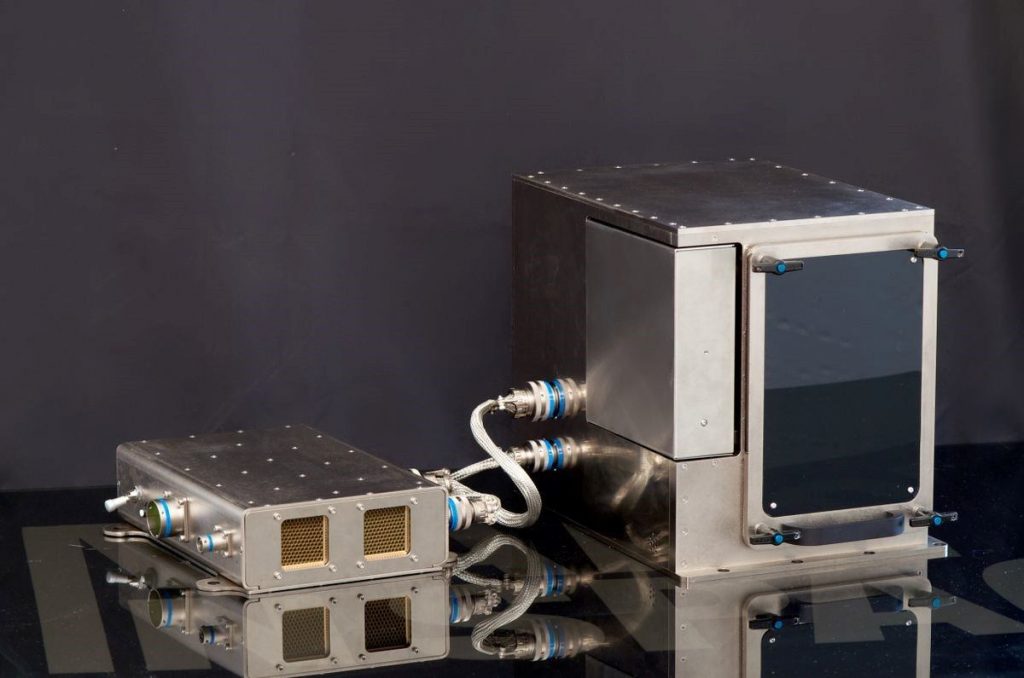
Rakétahajtómű
2013-ban a San Diegói Kaliforniai Egyetem hallgatói, a NASA-t és partnercégeit megelőzve, nyomtatott rakétahajtóművet terveztek és printeltek. Október 5-én az amerikai diákok a Mojave sivatagban sikeresen tesztelték a fémből nyomtatott, „Tri-D” névre keresztelt berendezést.
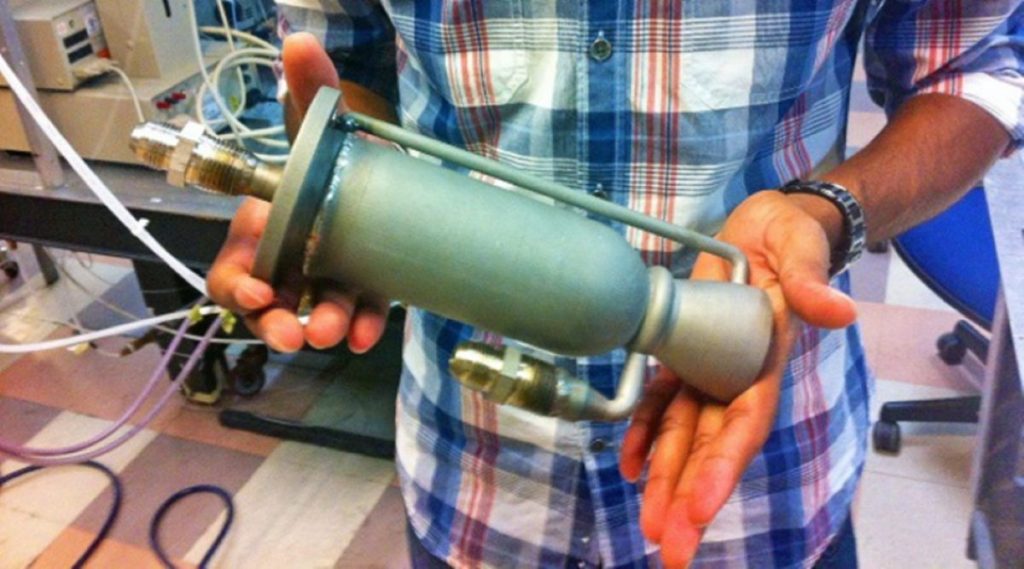
Történelmi pillanat a világűrben
A Nemzetközi Űrállomáson (az ISS-en), 2014. november 17-én az amerikaiak beüzemelték a Portal elnevezésű 3D nyomtatót, amelyet a Made in Space cég készített. A berendezést az űrállomás egyik mikrogravitációs dobozában helyezték el, majd a printerrel még ezen a napon próbanyomtatást végeztek.
Az első tesztfázisban – 13 hónap alatt – 25 alkatrészt a világűrben, 22 darabot pedig a Földön nyomtattak. Végeredményben az űrállomáson készített próbatestek mechanikai tulajdonságai sokkal jobbak voltak. Az első tesztfázis egy racsnis csavarkulcs elkészítésével zárult. Az előállítás érdekessége, hogy az STL fájlt (a nyomtatható modellfájlt) a Földről emailben küldték az űrállomásra, ahol a 42. küldetés parancsnoka, Barry Wilmore nyomtatta ki az eszközt.
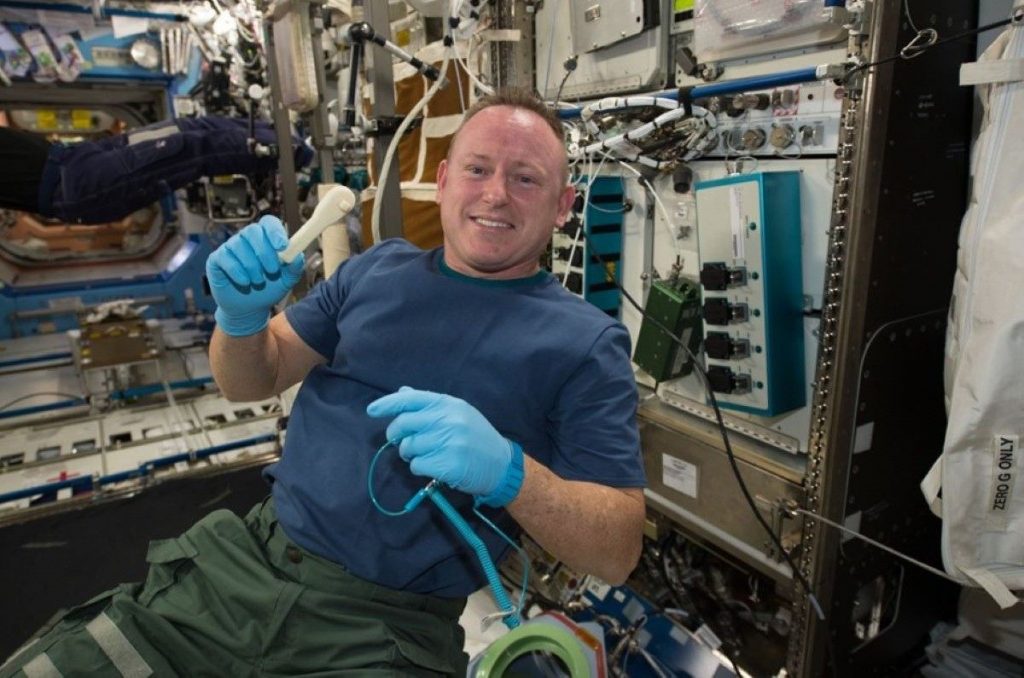
AMF – Made in Space
A Made in Space-nél a fejlesztések később sem álltak le. 2016-ra elkészítették a Portal jóval fejlettebb változatát, az Additive Manufacturing Facilityt (AMF-et), amellyel már többféle műanyagból (rugalmas polimerekből, repülőgépipari minőségű kompozitokból) lehetett tárgyakat nyomtatni. A berendezés 2016-ban került a Nemzetközi Űrállomásra, 2019-ig összesen 115 különböző eszközt printeltek vele.
Robotkar a Nemzetközi Űrállomáson
A Robai Cyton Gamma robotkar a Cygnus űrhajóval 2016. október 23-án érkezett meg az ISS-re. A kar tömege 1,2 kilogramm, anyaga pedig a Stratasys által kifejlesztett ABS Plus nyomtatószál volt. A kar felszerelése hagyományos megoldással 70 óráig tartott és 7 ezer dollárba került volna, azonban a térbeli printelésnek köszönhetően csak négy munkaórát vett igénybe, továbbá mindössze 400 dollárt kellett költeni rá.
Teherhordó rakéta három nap alatt
A kaliforniai székhelyű Rocket Lab 2017. május 25-én, Új-Zélandon sikeresen fellőtte első tesztrakétáját, amelynek hajtóművét 3D nyomtatással állították elő. A 20 méter hosszú Electron Rocket karbonötvözetből készült.
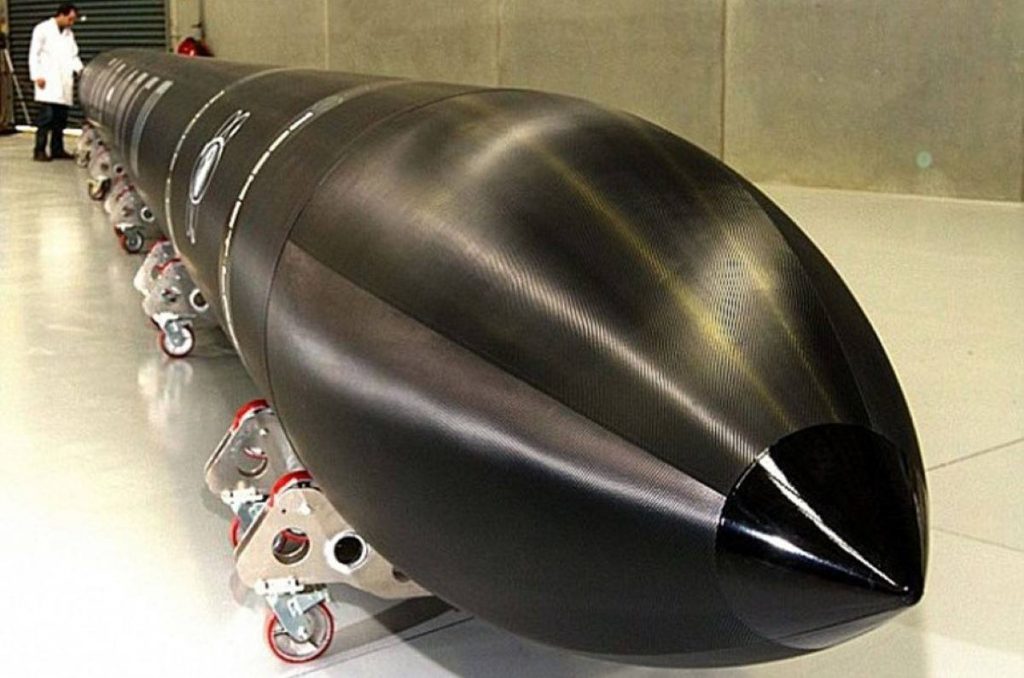
A teherhordó rakéta Nap körüli pályára 100, míg Föld körülire 400 kilogrammos szállítmányt képes eljuttatni. Az új rakétatípus sorozatgyártásra is alkalmas, a karbontestnek és a 3D nyomtatásnak köszönhetően akár három nap alatt elkészíthető. És ami ugyancsak meggyőző: a Rocket Lab rakétái öt esztendőn át összesen 30 küldetést teljesítettek.
Következő írásunkban a 3D nyomtatás további, űrkutatáshoz kapcsolódó megoldásaival foglalkozunk.
A nyitókép forrása: depositphotos.com